The road to a sustainable and profitable lens production
Meeting the needs of the present without compromising the ability of future generations to meet their own needs.¹
Sustainability includes not only examining the environmental impact of production, but three other pillars weighted equally: economic; environmental; and social factors. For this reason, finding ways manufacturers can produce competitively priced products that satisfy human needs and bring quality of life while progressively reducing environmental damage is key.
¹ United Nations General Assembly (1987) Report of the World Commission on Environment and Development: Our Common Future.
Eco-efficiency is one of the main tools to promote a transformation towards sustainability. It is achieved through progressively reducing environmental impacts and resource usage throughout the entire product life cycle to a level at least not exceeding what planet Earth is capable to give.
No doubt - industrial production is one of the biggest users of resources. According to the United Nations World Water Development Report 2019, 40% of all fresh water in Europe is used for industrial and energy production - 20% worldwide. This makes industrial production the second biggest user after agriculture. To improve eco-efficiency in lens manufacturing it is crucial to minimize the amount of hazardous waste, water and energy per good lens produced.
While producing approx. 600 million lenses per year, global Rx Labs are creating around 40,000 tons of swarf, using 4,800,000 m³ of fresh water and 1,800 MWh of electrical energy. Putting this into perspective, the amount of swarf is almost four times the weight of the Eiffel Tower, while the water can fill about 2,000 Olympic size swimming pools, and the amount of energy could power all of Paris for one month. In addition, this does not even consider semi-finish production, logistics and other steps in the overall product life cycle.
Exploring how new and green technologies, smart machines and the Internet of Things (IoT) enable Sustainability 4.0 through eco-efficient manufacturing, we find that reduction of the environmental footprint by using less physical materials and natural resources contribute to a sustainable lens production. Beside this, the continued use of alloy in ophthalmic production exploits precious materials and releases toxic remnants into the environment making its reduction especially desirable.
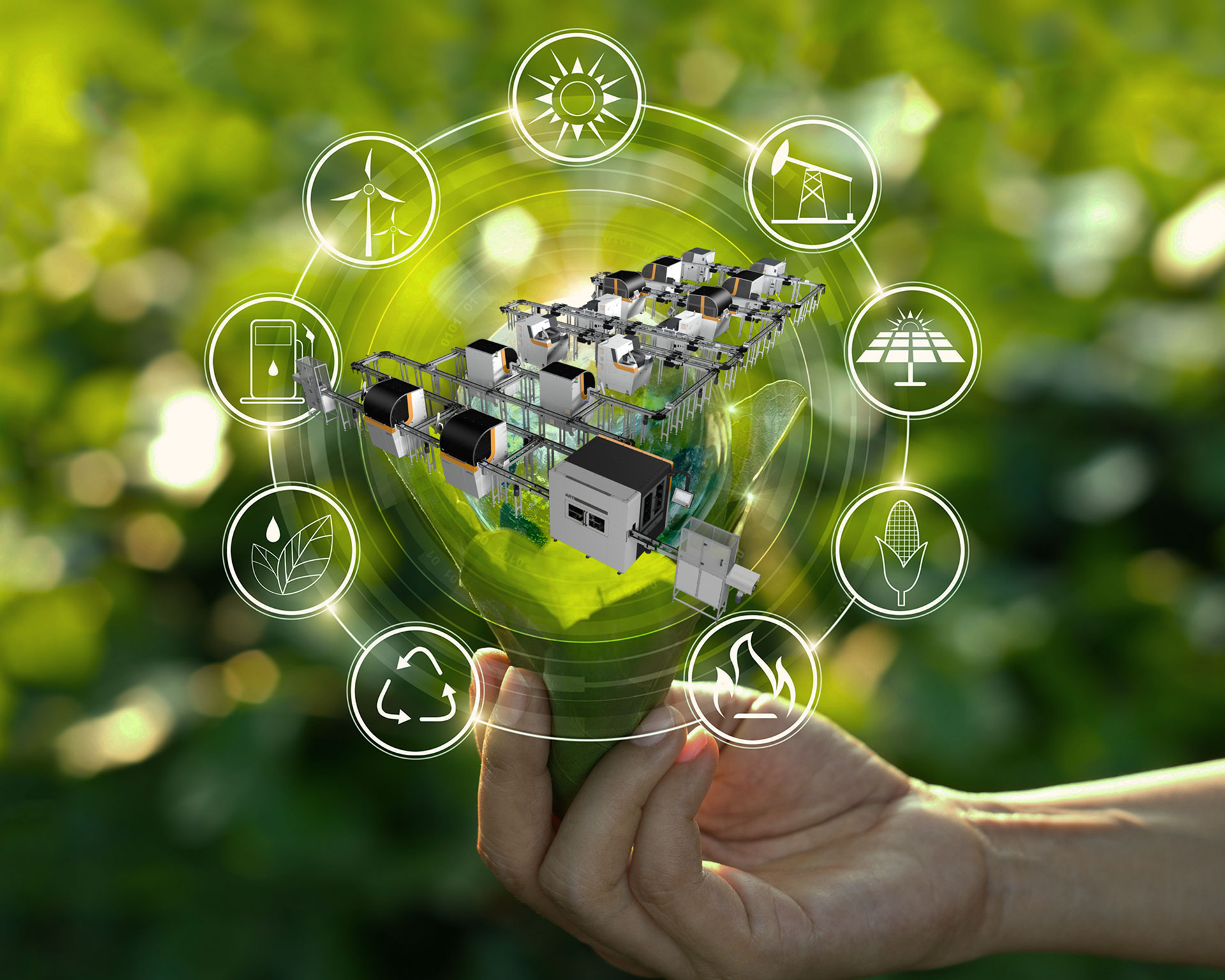
Target setting: walk a tightrope Eco-efficiency is not only environmental protection, but also producing competitively priced products with minimized environmental impact –so target setting is critically important.
Publicly traded companies of all industries utilize sustainability and eco-efficiency as major competitive advantages. Essilor states on their web page goals of reducing water intensity by 20% and energy intensity by 15% compared to a 2015 baseline. Zeiss just recently announced becoming Carbon-Neutral globally by 2025.
To achieve ambitious target setting, labs need to remember that scrap is double waste, so increasing yield as much as possible helps - along with using latest generation equipment. Alloy replacement technologies easily reduce the emission of toxic substances to zero, another opportunity to decrease the environmental footprint of lens production.
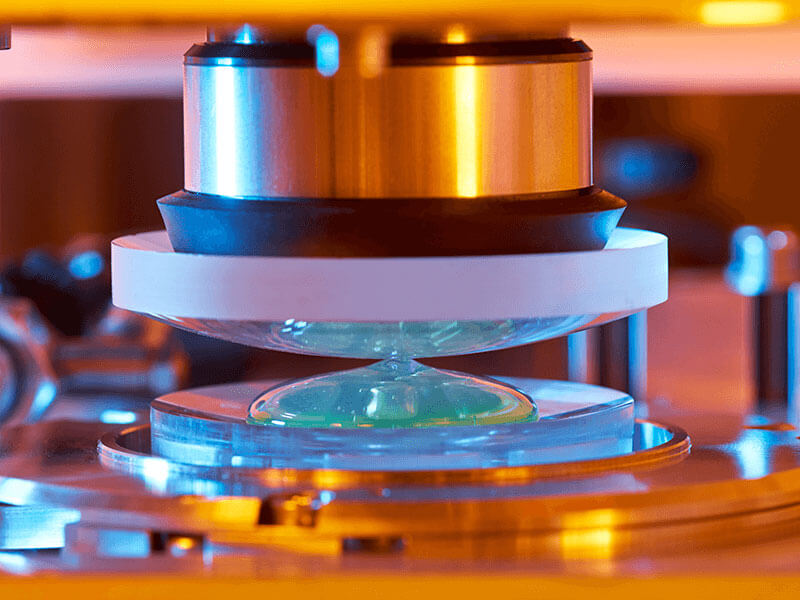
Minimizing hazardous substances with ART
Life cycle assessment (LCA) using a simplified study inspired by ISO 14040/14044 standards shows that not water or energy, but hazardous substances released into the environment as a result of alloy use is the biggest culprit. Cadmium concentration in alloy can be 40 times higher than allowed for wastewater. According to the LCA calculations, the environmental impact of alloy remnants is 60 times higher compared to that of waste, water, and energy.
Lens blocking with ART offers an environmentally friendly alternative to traditional alloy blocking.
Since the introduction ART (Alloy Replacement Technology) through June 2020, it has saved around 37,400 kg alloy going into swarf and waste water (assuming that for every alloy-blocked lens the loss of alloy is on average 0,4 grams). Approximately 5% of alloy is pure cadmium, so reducing alloy use combined with lowering energy usage and decreasing waste and water in lens production will significantly bring down the stress on Earth’s natural resources.
ART machines are the next generation of equipment that will help labs move towards eco-efficient production. With the ART-Blocker/Deblocker arrangement, labs will see up to 50% lower energy consumption compared to the four pieces of equipment alloy requires. Furthermore, ART machines do not have an alloy tank heater or cooling plate, which means even less energy consumption.
Adding a water filtration system to the deblocker recirculates water back into the system, reducing water consumption by up to 80% through. As such, there are also 99.99% less emissions of toxic lead and cadmium and no micro plastics due to the elimination of surface saver tape in the ART process.
Managing swarf waste
Plastic waste is a global problem; swarf, scrap and cardboard account for over 50% of waste in lens manufacturing. Only pure polycarbonate with low contamination can be recycled, the re-use of thermosetting polymers (CR39 and Hi-Index) is only possible to some extent. Bringing swarf from the machine back into the recycling loop can be a challenge, and segregating swarf after processing a material mix in one machine is even harder. The following help recycle swarf:
- Segregated processing
- Briquetting for easier recycling and less coolant loss
- Recycle thermoplastics like polycarbonate
- Reuse thermosetting polymers like CR39 for specific applications
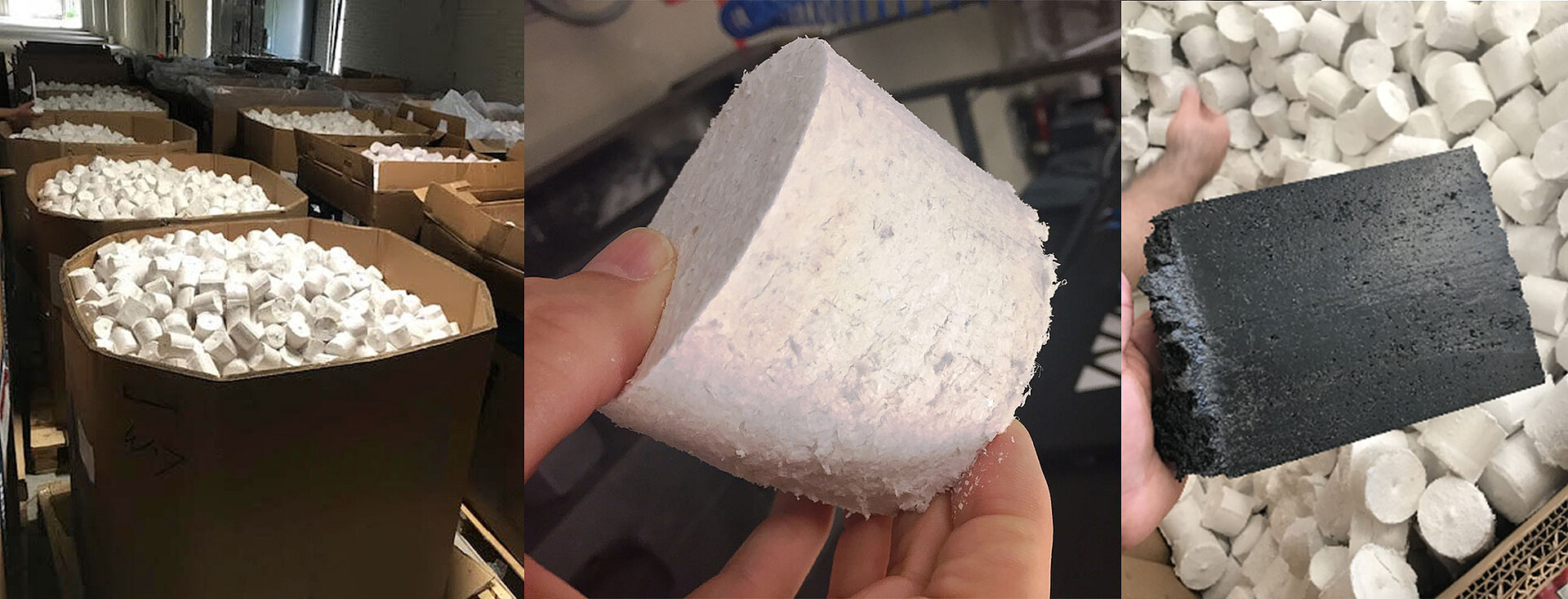
In a study at a large lab with 24/7 operation and producing mixed blank substrates, we observed savings of approximately 38% in water and coolant consumption as a result of using automated chip, coolant management and micro separating systems together with a briquetter press that compacts swarf. With this method, the swarf weighs significantly less because of water extraction, and reduces waste volume with a ratio of 12:1.
Finally, it also increases productivity because labs can eliminate manual chip removal at the surfacing step and expand its capacity with less cleaning time required.
Becoming more sustainable: A multi-level approach
To reduce resource intensity a multi-level approach is the most promising and efficient way to become more sustainable. Starting from production processes optimization for yield and throughput, leveraging on efficient equipment using green technology. Furthermore, intelligent automation ensures a smooth and flexible flow and even looking into green building management are great ways to become more sustainable without sacrificing economic efficiency. On the other hand – using lean production methods, automation and up-to-date machinery to push flexibility, yield and productivity will even help profitability of the lab
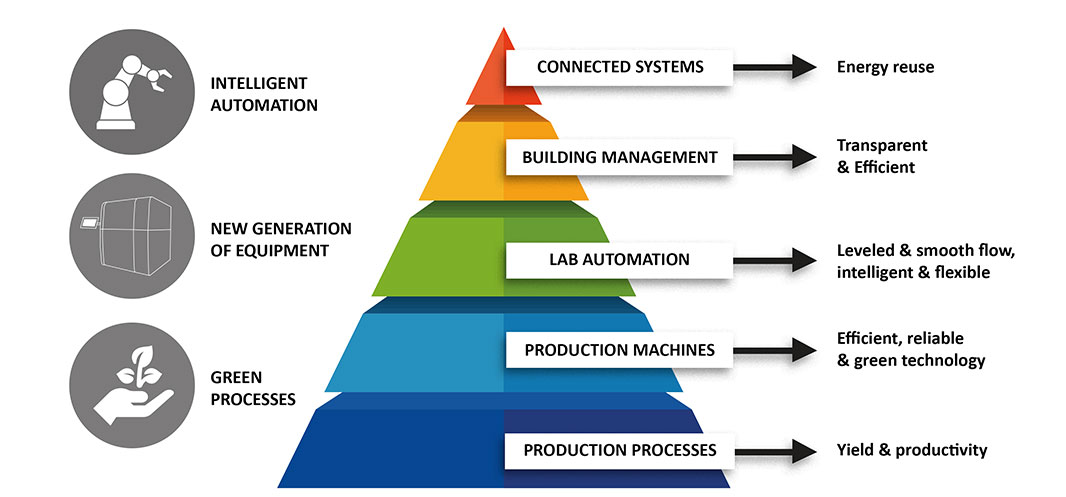
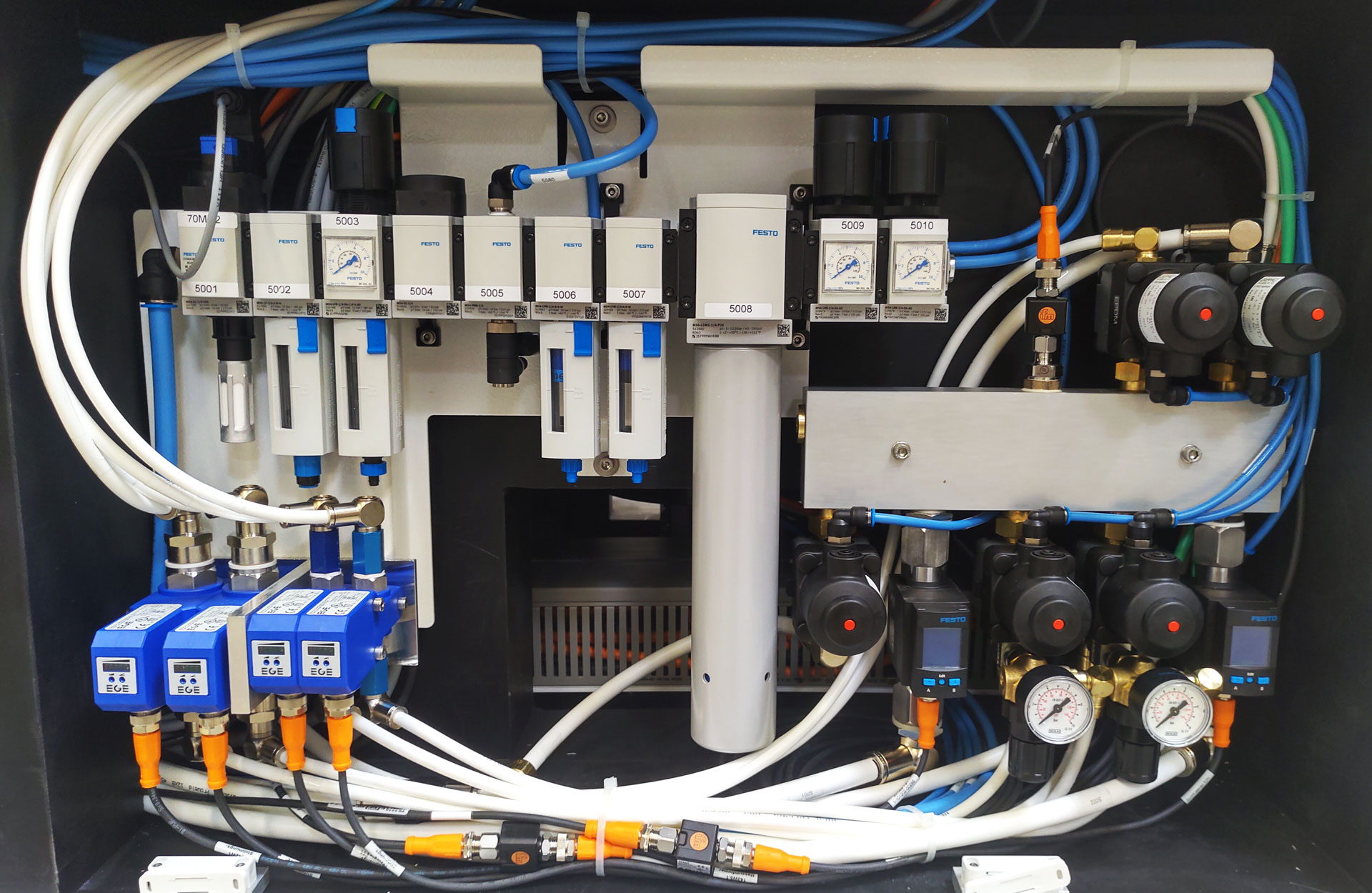
Smart machines ensuring maximum yield to minimize energy waste
Why is a lean production approach so important? Waste is not only physical products; it is also non-essential movement, redundant processes and time lost while waiting, which decreases productivity and thereby wastes valuable energy. Maintaining a lean production philosophy will boost eco-efficiency and applying these production principles will allow labs to control the resource consumption.
Yield and uptime are critical because efficiency and resource intensity is defined by resource input per good product output. However, by having a machine switched on and kept at a stable temperature, with no throughput, valuable energy resources are wasted. Yield is crucial as the scrap is double waste and consumption. Using the latest technology with smart machines enables a lab to control these parameters for maximum efficiency.
Smart machines constantly monitor conditions and performance indicators, which enables predictive, conditional, or self-maintenance. Keeping on top of machine maintenance is another way to ensure production uptime and peak performance. Smart machines will use conditional maintenance, which monitors indicators that show signs of decreasing performance as well as self-maintenance where monitoring of conditions and performance indicators facilitate the machine to self-adjust its processes.
The conditional and self-maintenance will help strengthen uptime and manage downtime efficiently by using sensors and employing internal logics to bring down breakage and optimize throughput. It helps labs lower waste and thereby become more eco-efficient. DATA DRIVEN INSIGHTS FOR OPTIMAL MACHINE UTILIZATION Certainly with common sense, experience and pure lean production methodology a very reasonable level of quality, yield and uptime, and therefor eco-efficiency, can be reached. To push lab operations performance to the maximum, we need to look at IoT, big data and real-time systems. As Peter Sondergaard stated as SVP at Gartner already in 2011: “Information is the oil of the 21st century, and analytics is the combustion engine.”
Investing in Lab 4.0 ready machines will reduce labor, be more cost efficient, provide faster delivery, show less breakage, have a smaller footprint per job and see less energy consumption.
Every process in manufacturing generates valuable data. However, as we learned data alone means nothing - it becomes precious when refined through a manufacturing execution system (MES), which translates raw data into usable information. An MES, such as Satisloh’s MES-360, enables manufacturers to make smarter decisions and in return, the business becomes more efficient as a whole and therefore more profitable.
Setting up dynamic rules to close the control loop means when the system detects a machine cannot process a certain lens, MES re-routes those jobs only to machines that have this capability. Consequently, implementing MES will help streamlining production by providing the highest utilization of available machine and show improved flexibility and productivity. It will guarantee faster throughput and delivery times as well as lower tool costs because jobs are routed to specific machines that are optimized for them.
Optimizing breakage through MES leads to reduced waste. Analyzing the data captured in MES, allows lens manufacturers to track problems back to specific machines, lens materials, Rxs or other factors. It helps labs react faster when breakage alerts arise, and the information is used for dynamic routing of the jobs, resulting in higher yields and lower costs, while increasing eco-efficiency.
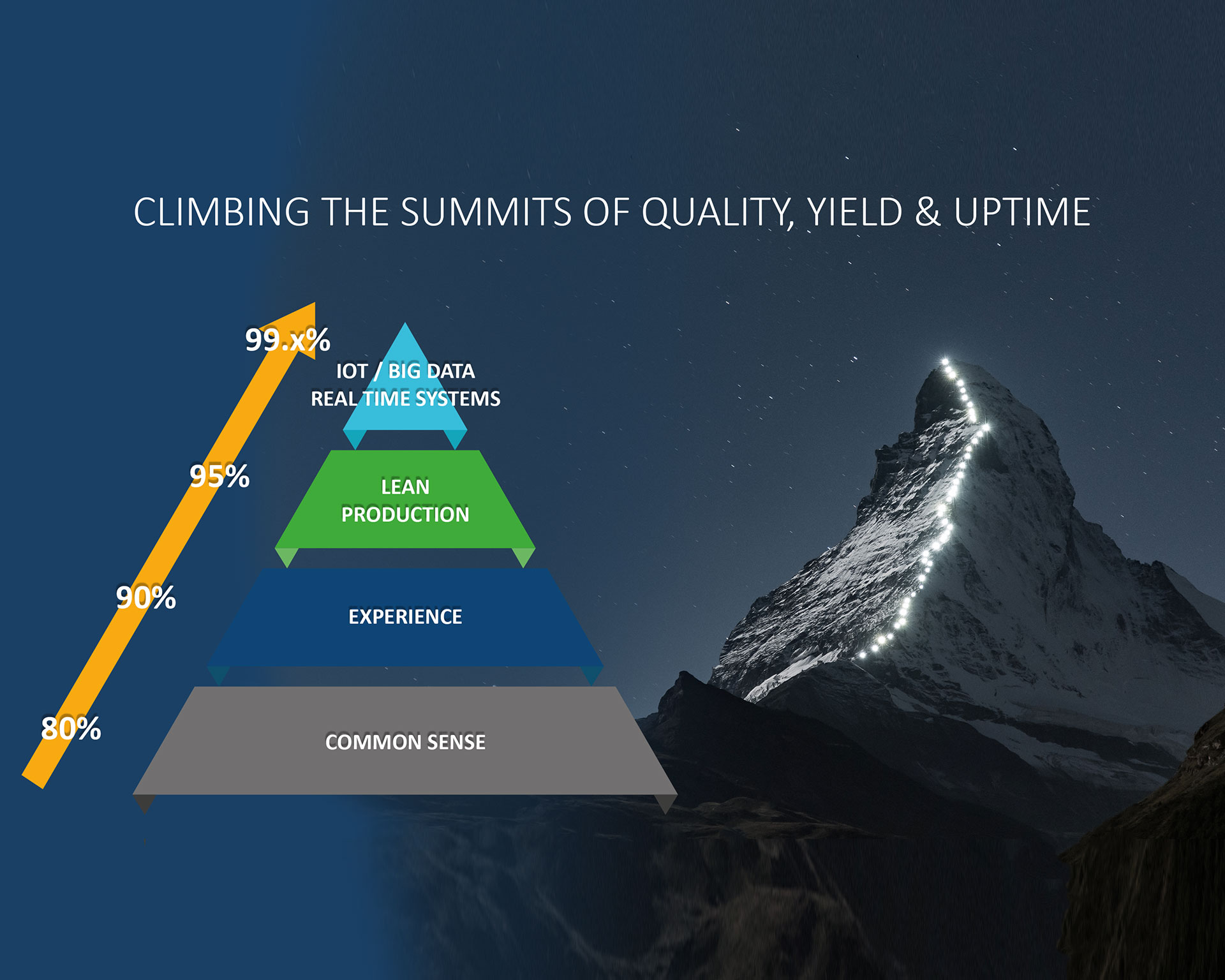
Sustainability 4.0 through eco-efficient lens manufacturing
Ensuring labs produce lenses at the highest possible eco-efficiency means reducing waste, water and energy consumption through optimized processes that provide excellent throughput, high yield, and optimal uptime. Combining data and intelligent automation will help eliminate waste and heighten effectiveness. Full transparency of lens production requires an open system on a data level with machines connected through IoT.
Every Lab 4.0 ready machine on the production floor can be connected an MES, allowing manufacturers to run their lab at maximum capacity. The system connects, communicates and exchanges information with all machines in the lab, regardless of the machine manufacturer –and if desired even the coffee machine. The overall goal is to reduce the lab’s environmental footprint and through smart machines and the right technology, we see an opportunity to minimize waste volume, improve water usage, and minimize energy consumption - and inevitably create sustainability 4.0 through eco-efficient lens manufacturing. Moreover, all this without sacrificing the profitability at all.
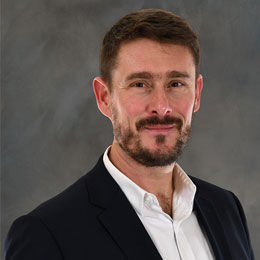
An article by:
Dr. Michael Kreis
Vice President of Global R&D, Satisloh Group
Ask us a question
Satisloh experts are ready to answer your questions. We help you make the right machine purchase decision
Request product information
Satisloh designs and manufactures machines that meet your specific requirements. Request more product information or your personalised quote today!